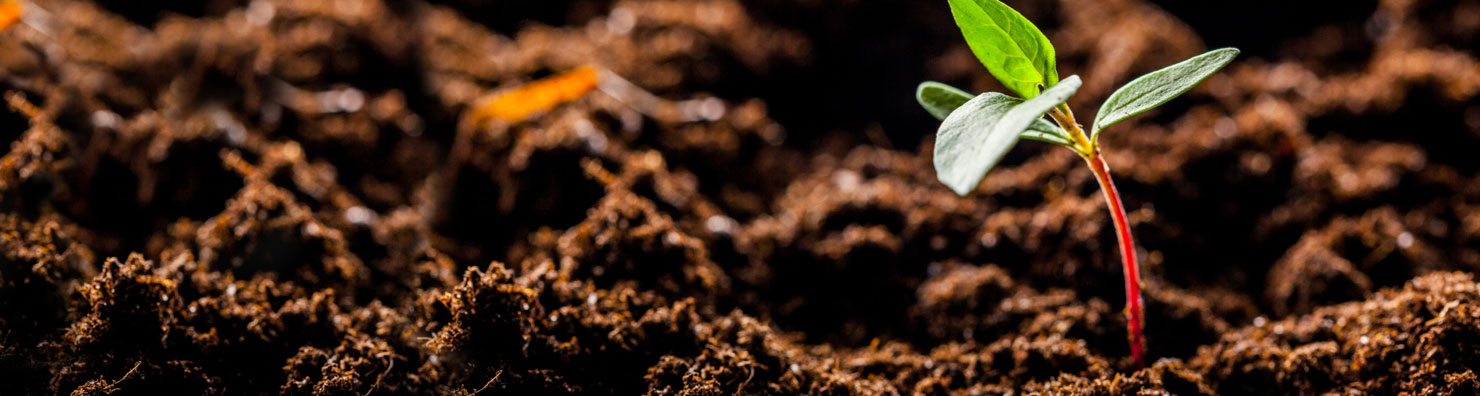
Composting is an aerobic bi-oxidative process made by organic matrices. The process is promoted by micro-organisms that are usually present in the environment and that are essentially attributable to three main categories: bacteria, actinomycetes and fungi.
Bacteria are primarily responsible for generating heat during the process of decomposition and, usually, they are quick decomposers that are able to use the most rapidly degrading substances and the intermediate products of fungal metabolism.
Actinomycetes deteriorate complex substances, such as proteins, celluloses, hemicelluloses, chitin and lignin and they are primarily responsible for the characteristic smell of earth released by matured compost.
Fungi deteriorate complex molecules, such as waxes, hemicelluloses, pectin and lignin, in order to make intermediate products available to metabolic bacteria, as they would not be degradable in other ways.
The industrial composting process, such as the one carried out by BIOFACTORY plant, repeats the natural humidification process active undergrowth in a shorter time and it is checked in order to improve natural mineralisation and humidification of the organic matter. The aim is to obtain a product that is biologically stable and mature. The matrices subject to composting treatment are: green maintenance residues and wet waste deriving from waste differentiated collection. First of all, matrices are mashed and mixed according to a constant volumetric ratio equal to 1:3 (wet: green) and they are later sent to compost.
The composting process is essentially made up of two phases:
This first step is characterised by a mesophilic initial phase, during which the mass is invaded by micro-organisms, and a second thermophilic phase of strong bi-oxidation: in the first place easily fermentable organic molecules are decomposed, such as simple sugars, amino acids, organic acids…etc. The most complex molecules are decomposed at a later stage. Bio-oxidation process takes on average 40-50 days and it takes place inside the closed warehouses for wet-green mixture and outdoor for green residuals only. The material is arranged in windrows that are periodically turned using a mechanical shovel. Turning of windrows guarantee the material mixing, favouring the decomposition of agglomerates and the recovery of the porosity of the matrix being transformed; the result is a homogeneous stabilisation of the material after a cyclical variation of the oxygen inside the accumulation. The high temperature (65°-70° C) reached in the fermenting mass completely sanitise the material and guarantee the disappearance of pathogens, weed-seeds and any phytotoxic elements. At the end of this first phase the product obtained undergoes a refining treatment that reduces the presence of extraneous materials or of non-composted wood residues.
During the 1st dynamic maturation phase, the material, that is distributed in accumulations outdoor, completes the humidification process of the organic matter thank to the action of mesophilic microbial populations. The minimum active maturation period is of 50 days; during this period, the mass is constantly turned in order to guarantee a proper level of the oxygen that is necessary for the microbial activity. BIOFACTORY S.p.A. characteristics is that the maturation phase is prolonged for over a year. This 2nd maturation phase, static without any mass turning, is preceded by a first mechanical selection that allows to eliminate the part of ligno-cellulosic material that is not composed yet. Such material goes back to the process first phase. We also eliminate any components that cannot be composed (plastic, metal, glass) that were into the input matrices and that return to their specific waste recovery cycle. Such maturation lengthening leads to a particularly strong humidification of the organic matter, with the guarantee toobtain a very stable product with high content of humidified organic matter (humic and fulvic acids). Before being marketed, the compost undergoes a further mechanical selection and screening, in order to obtain extremely clean and homogeneous material. The treatment of exhausted airs sucked from FORSU reception and bi-oxidation locals is performed through a double humid layer scrubber, an acid-base system that can absorb, oxidise and salificate odour-causing molecules contained into the exhausted airs. The leachate that originates from the various manufacturing phases is collected into a special tub; in summer or in case of need to increase the mass humidity during the bio-oxidation phase, we recycle sewage on the composting cumulations inside the closed warehouse.